Автор кейса:
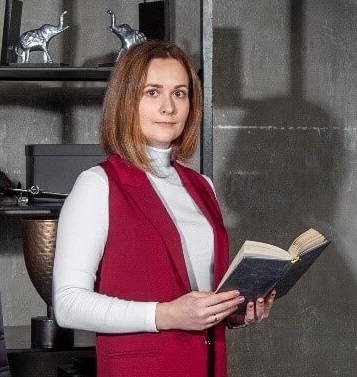
Анна Гончарова
директор по развитию ООО Профконсалт ИСМ
Действующие лица
Клиент — Московская пивоваренная компания (МПК)
Московская Пивоваренная Компания вышла на российский рынок напитков в сентябре 2008 года. Компания предлагает рынку широкий ассортимент пива и безалкогольных напитков собственного и лицензионного производства: «Жигули», «Трехгорное», «Хамовники», Gorilla Energy.
В состав компании входят современный пивоваренный завод, а также собственные дистрибьюторский и логистический центры, расположенные в г. Мытищи в экологически чистом районе. Завод МПК имел первоначальную производственную мощность 2,4 млн гл в год, сегодня возможности производства составляют 8 млн гектолитров в год. МПК девять лет активно развивалась и росла, каждый год увеличивала на 15-20% продажи и производственные мощности. На стадии экстенсивного роста силы были направлены в основном на инвестиционные проекты.
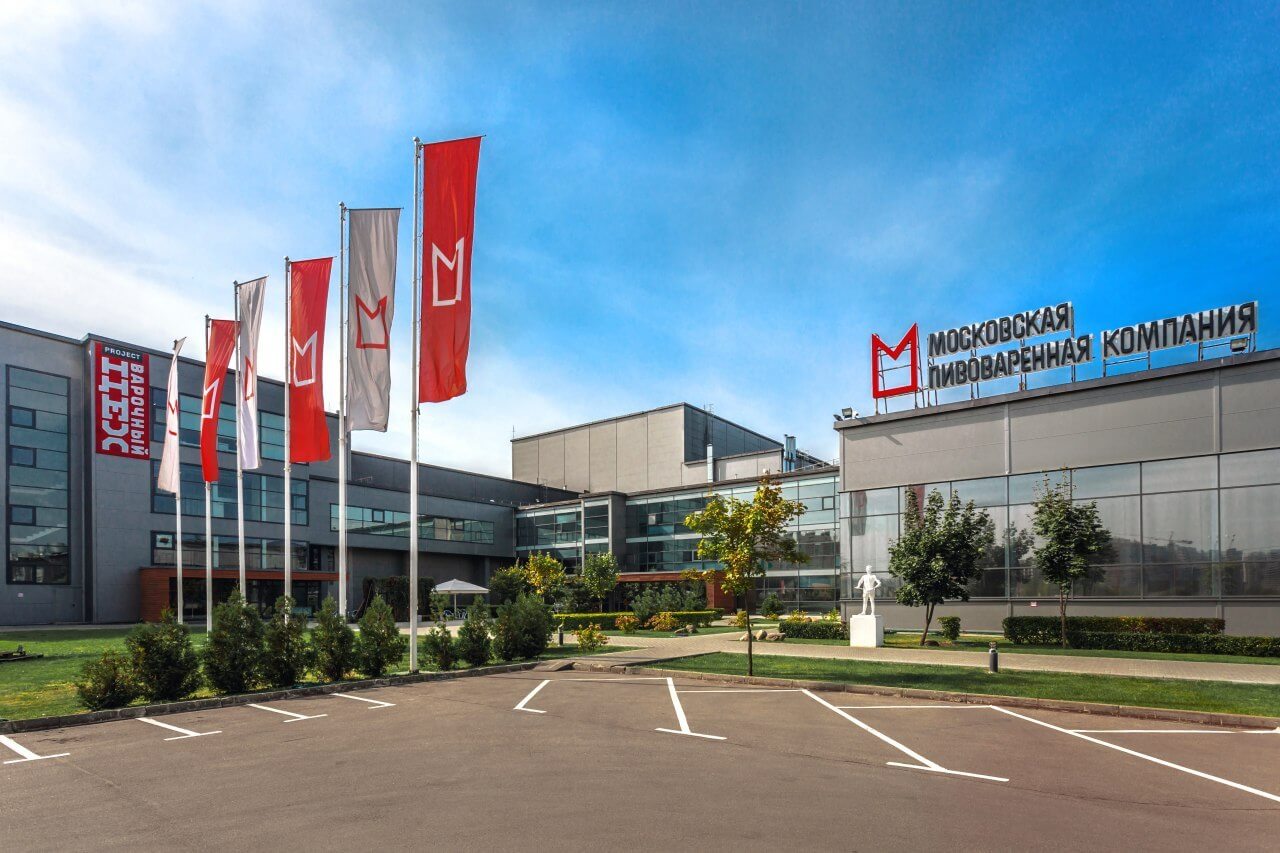
Исполнитель — ООО Профконсалт ИСМ
Работаем на рынке консалтинга со средним и крупным бизнесом с 2010 года. Внедряем, чиним и поддерживаем производственную систему и/или её элементы, проводим открытые и корпоративные обучения, учитывая индивидуальные условия заказчика.Мы постоянно повышаем качество услуг и превышаем ожидания Заказчиков по нашим технологиям и результатам.
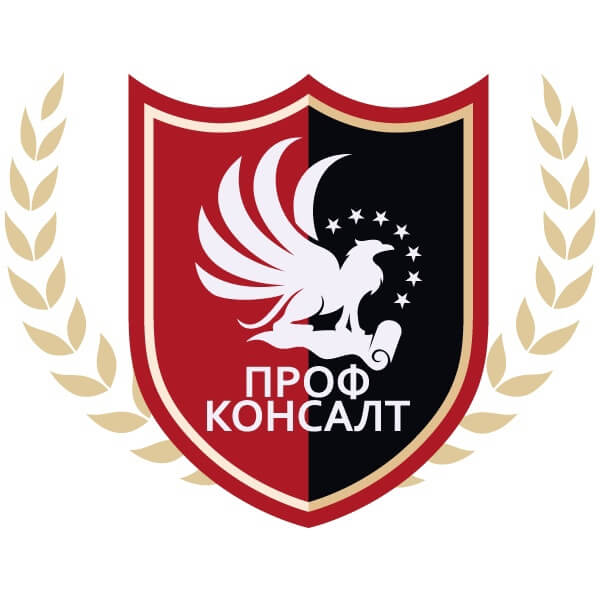
Задача
К 2018 году Московский пивоваренный завод стал самым крупным в своей отрасли в РФ и подошел к этапу, когда нужно повышать свою конкурентоспособность и оптимизировать производство:
- сокращать издержки;
- снижать себестоимость;
- повышать привлекательность продукции;
- увеличивать доступное время использования оборудования.
Клиент на тот момент реализовывал инвестиционные проекты, которые длятся от года, рассматриваются с точки зрения срока окупаемости и всегда связаны с большими затратами. Задачей Профконсалт ИСМ также было сократить издержки на реализацию проектов, уменьшить длительность проектов и срок их окупаемости.
Решение
МПК обратился в Профконсалт ИСМ с запросом на внедрение методологии Техническое обслуживание и ремонт оборудования (ТОиР). Мы провели первичную диагностику и предложили сосредоточиться на проектах Лин 6 Сигм, так как все задачи, которые озвучил клиент, закрывает именно методология Бережливого производства и производственной статистики.
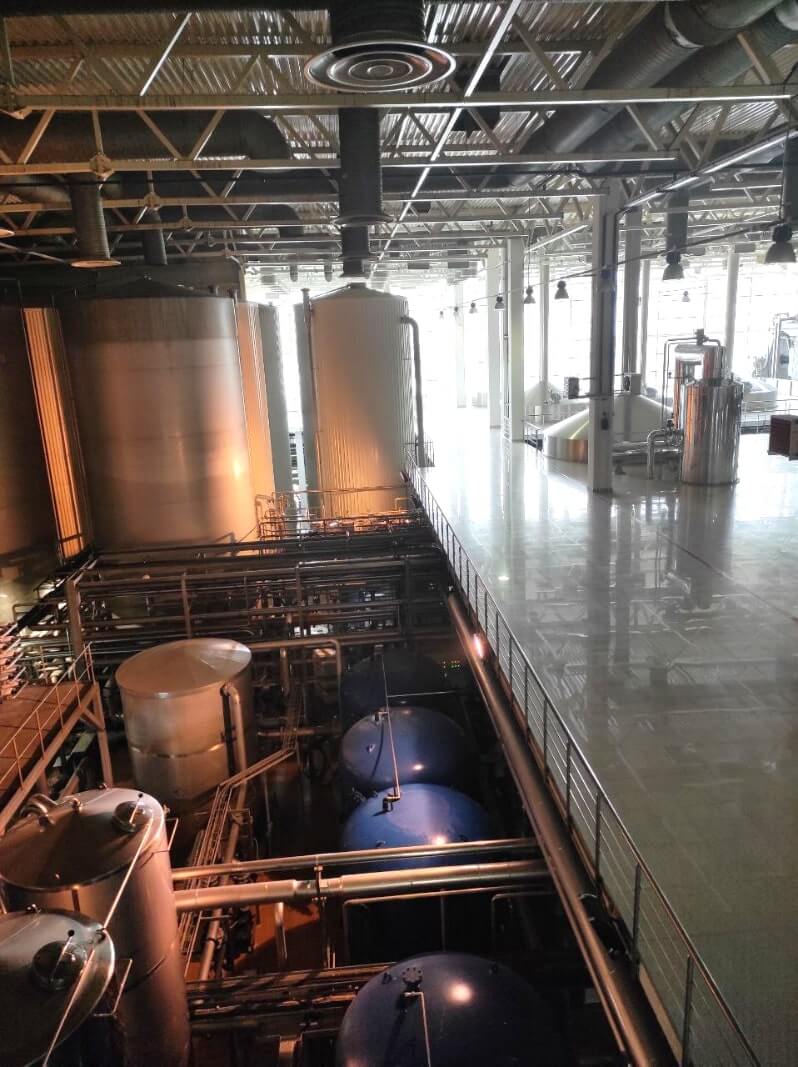
Оно включает в себя:
- проекты 5С (организация рабочего пространства);
- SMED (быстрая переналадка оборудования);
- ТРМ (всеобщее обслуживание оборудования) как начальный этап для ТОиР.
Преимущества проектов Бережливого производства:
- проекты короткие — от 3 до 6 месяцев;
- те небольшие расходы, которые компания несет за внедрение системы улучшений, быстро окупаются. По статистике, каждый проект бережливого производства окупается 2-5 раз в год.

Цель Бережливого производства — уменьшение всех видов потерь и, как следствие, увеличение добавленной стоимости бизнесу, процессам, деятельности.
Цель 6 Сигм — это обеспечение бездефектного выпуска продукции путем уменьшения изменчивости (нестабильности) процесса.
Целью методологии «Лин 6 Сигм» является улучшение функционирования организации, а также получение более высокой прибыли путем решения проблем бизнеса, которые, возможно, существовали в течение длительного времени. Движущей силой этого подхода является стремление организаций к повышению конкурентоспособности и устранению ошибок и потерь.
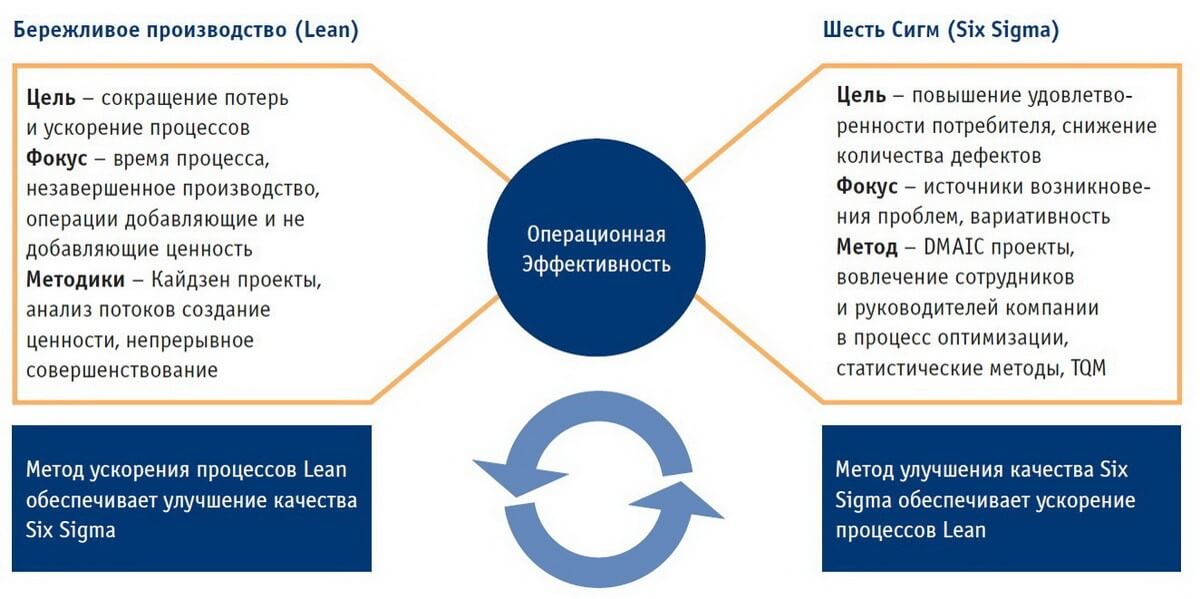
С какими сложностями столкнулись?
Отсутствовала базовая подготовка у сотрудников компании-клиента и знания по статистическим данным. Не у всех сотрудников было понимание того, что такое, например, сигма и первое квадратичное отклонение (показатель рассеивания значений случайной величины).
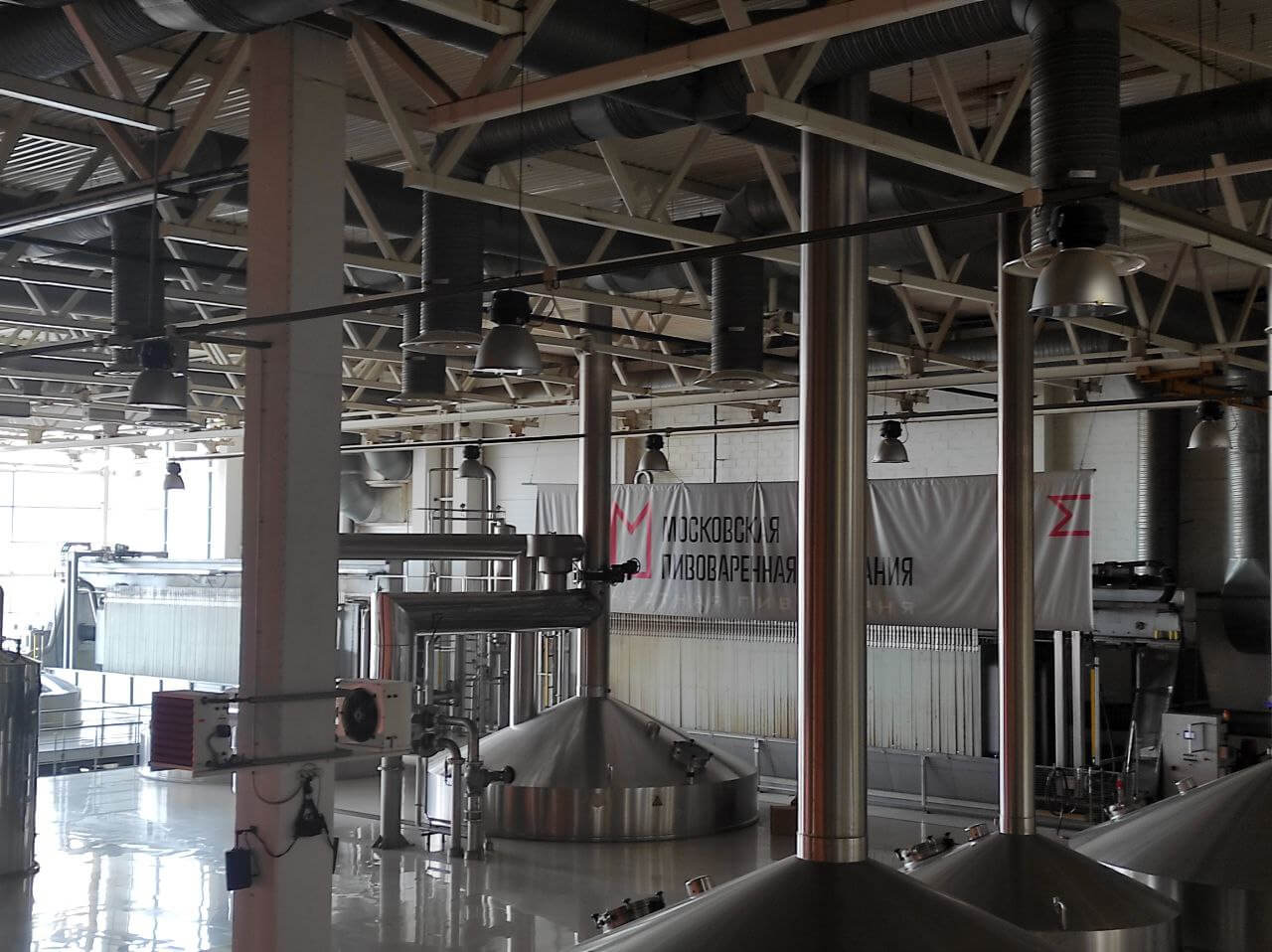
Что мы сделали?
В 2018 году мы начали внедрение концепции Бережливого производства. Начали с основ: провели ликбез по теории и методам внедрения инструментов Бережливого производства.
1. Провели обучение «Зеленые пояса» для лидеров будущих рабочих групп.
Тренинг «Зеленые пояса» проводится для подготовки специалистов по бережливому производству, устранению потерь, повышению производительности и обучения основами производственной статистики и теории ограничений.
Среднестатистические результаты после завершения тренинга:
- Реализованные проекты: не менее 1-го на каждого из 18 обучающихся.
- Эффект не менее 2 млн.руб. каждый или 1*18*2 = 36 — 20% = 28,8 млн.руб на группу.
- Подготовленные специалисты-практики, способные решить задачи бережливости на производстве на основе проектного управления.
Итак, на первом этапе нашей работы с Клиентом мы определили состав группы из 15 человек для обучения — будущих лидеров рабочих групп. Эти сотрудники на время обучения были частично отвлечены от основных обязанностей.
2. В рамках обучения «Зеленые пояса» мы выбрали 12 самых эффективных проектов — простых и выгодных.
Проекты выбирались по темам, связанным с основной производственной деятельностью сотрудников. В процессе обучения и перед началом реализации проектов, лидеры рабочих групп начали передавать полученные знания об инструментах Бережливого производства и производственной статистике коллегам, привлекать остальных в проекты, формировать рабочие группы. То есть лидеров было 15, а в результате вовлекли в систему около 50-60 человек, которые совместными усилиями реализовали проекты и продолжали распространять информацию о методологии по предприятию.
12 проектов бережливого производства
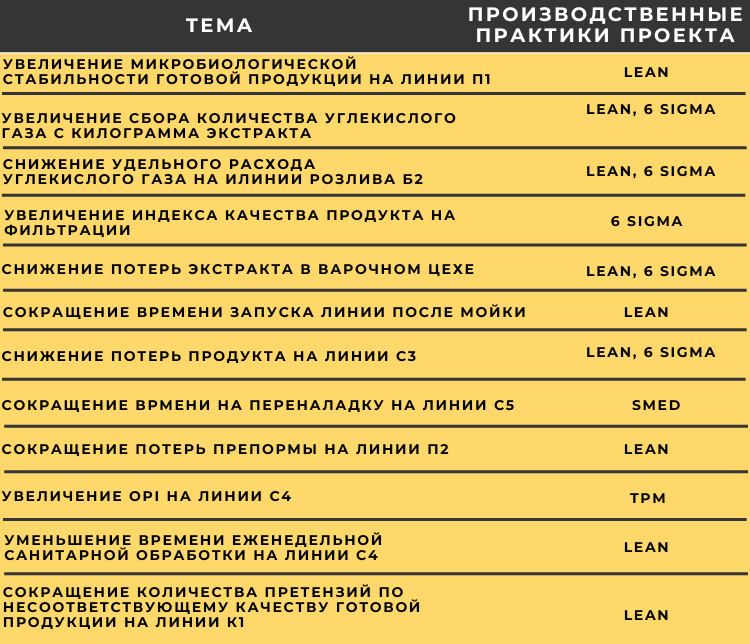
3. Начали внедрение инструментов с базы — системы 5 S.
Важно сначала навести порядок на рабочих местах, поддерживать его, а затем уже оптимизировать и улучшать. Потому что улучшить что-либо в хаосе невозможно. Кстати, система 5 S применима не только на производстве, но и в любом бизнесе, в любом офисе. Почему мы начали с внедрения 5 S:
- Только после систематизации можно внедрять более сложные методики.
- После внедрения 5 S можно добиться прогресса по таким направлениям как «ТРМ», «SMED», «Стандартизованная работа».
- 5 S создает «фундамент» бережливого производства и обеспечивает стабильность процессов. Отсутствие порядка будет фактором, который будет постоянно увеличивать вариабельность всех процессов и сводить на «нет» все ваши достижения.
Внедрить 5 S не сложно (многие предприятия внедряют её по несколько раз), сложно поддерживать и улучшать 5С, добиться того, чтобы система стала привычкой. Причина простая: невозможно внедрить и поддерживать 5С, если вы не измените свою культуру, не измените себя.
Что стало залогом успешного внедрения?
- Провели аудит по системе 5 S.
- Внедрение 5 S — это не разовая акция, а постоянный труд. Мы поддерживали и улучшали 5 S в течение всего проекта по Бережливому производству.
- Внедрение 5 S невозможно без поддержки и активной вовлеченности в процесс высшего руководства. Для поддержания созданного процесса обзавелись поддержкой и активным участием высшего руководства компании.
- Информировали и вовлекали персонал в процесс улучшений через высшее руководство и лидеров рабочих групп.
- Замотивировали высшее руководство вдохновлять и вести за собой коллектив, быть для него примером.
- Поделились реальным опытом и кейсами других предприятий.

4. Реализовали проекты с использованием инструментов Лин (SMED, TPM, Карта потока создания ценности, FMEA)
- Снизили процент инфицирования готовой продукции на линии ПЭТ-1 за год до 7%. Достигли отсутствия возвратов и претензий на готовую продукцию из торговой сети (клиентов) по причине несоответствия микробиологическим показателям.
- Сократили время проверки чистоты оборудования и порядка на линии стекла.
- Оптимизировали время работы химиков и микробиологов.
- Сократили время переналадки оборудования с 5 до 2,5 часов.
- Сократили потери преформы на линии розлива с 10,3% до 3,1%.
- Повысили производительность линии с 32% до 40% в среднем за год.
5. Реализовали проекты с использованием инструментов 6 Сигма (производственная статистика)
- Увеличили сбор количества углекислого газа с килограмма экстракта.
- Достигли увеличения индекса качества напитков с 97% до 99%.
- Сократили потери экстракта в варочном цехе до с 2,1 до 1%.
Результаты
За 5 лет с момента внедрения Бережливого производства в компании:
- Средний экономический эффект (сэкономленные средства) от 1-го проекта — 4 млн рублей.
- 36 реализованных проектов.
- Общая сумма экономического эффекта от реализованных проектов — 150 млн рублей.
«Внедрить бережливое производство – это не значит стать просто бережливым, а это значит сделать свою компанию компанией без потерь. Потери – это не только материальные ресурсы, но и время, потери на неправильный порядок и организацию. Я не знаю много примеров компаний, где успешно бы внедрялся аналогичный проект своими силами. Такие примеры есть, но они неуспешны».
— Юрий Лобанов, директор завода МПК
Больше подробностей о кейсе в видео-формате:
так много терминов, что, если честно, я мало чего понял(((
Классный материал, давно задумывался о внедрении бережливого производства! Хотелось бы ещё на примере дроугих областей бизнеса разобрать